Cet article explique comment le fournisseur équatorien de technologies 3D BSTAR a utilisé la numérisation 3D pour la réfection de cloisons de bus. L’entreprise a scanné en 3D la partie problématique avec le EinScan HX et l’a redessinée dans Solid Edge.
Table of Contents
Introduction
Les chauffeurs de bus de Quito, en Équateur, sont exposés à un bruit excessif dans le cadre de leur travail en raison de pièces mal conçues dans leur habitacle. Ce problème, qui affecte leurs conditions de travail depuis des années, est présent dans des centaines de bus de la ville.
La municipalité a donc fait appel à BSTAR, un fournisseur équatorien de services technologiques, pour trouver une solution efficiente. Les ingénieurs de BSTAR ont utilisé le SHINING 3D EinScan HX et Solid Edge pour relever ce défi.
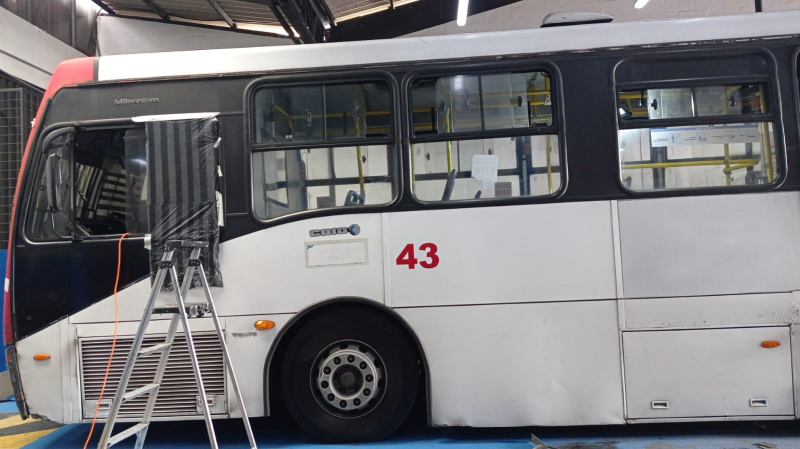
Nom : BSTAR (BSTARTECHNOLOGY S.A.)
Offre : Services de numérisation 3D et de conception 3D, vente d’imprimantes 3D
Localisation : Quito, Ecuador
Besoin : Réfection d’une cloison inadaptée qui causait un bruit excessif
Solutions : EinScan HX et Solid Edge
Résultat : Conception rapide et efficace d’une nouvelle cloison aux dimensions optimales
Une faute de conception affecte 800 autobus et leurs chauffeurs
La capitale effervescente de Quito compte plus de 2 millions d’habitants. Son système de transport public comprend plusieurs options : lignes de métro, chemins de fer, vélo-partage et bus.
Parmi ces options, le réseau de bus “Metrobus-Q” est une option populaire. Plus de 800 bus sillonnent la ville pour desservir ses 750 000 passagers quotidiens. C’est l’épine dorsale du système de transport de la ville et une excellente solution pour ses utilisateurs.
Cependant, du côté des conducteurs, les bus posent un sérieux problème.
Chaque bus est équipé de cloisons à côté du siège avant, destinées à séparer et à protéger le conducteur de la foule. Le problème est que ces cloisons ne sont pas totalement adaptées à l’habitacle. Ce défaut de conception entraîne un bruit de cliquetis excessif que les conducteurs doivent supporter 8 heures par jour.
Ce bruit affecte leur audition et leur bien-être depuis des années, et il est présent dans chacun des 800 bus. La municipalité de Quito a décidé de contacter l’équipe BSTAR pour une refonte complète des cloisons.
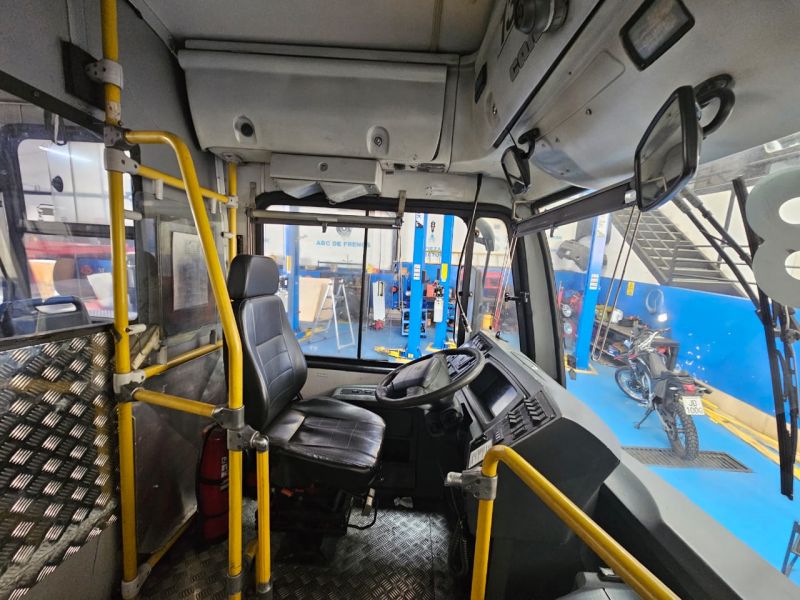
Numérisation 3D pour la réfection de cloisons de bus
Pour éliminer le bruit de cliquetis, BSTAR a dû mesurer avec précision le cockpit et concevoir une cloison sur mesure. Ils ont décidé d’utiliser le scanner 3D EinScan HX de SHINING 3D pour la prise de mesures.
Cette solution de numérisation 3D portable était idéale dans ce cas pour plusieurs raisons.
Tout d’abord, il était facile de l’emporter dans le bus, sans trépied ni installation complexe. Sa portabilité a également permis au technicien d’accéder aux espaces étroits autour et sous le siège du conducteur.
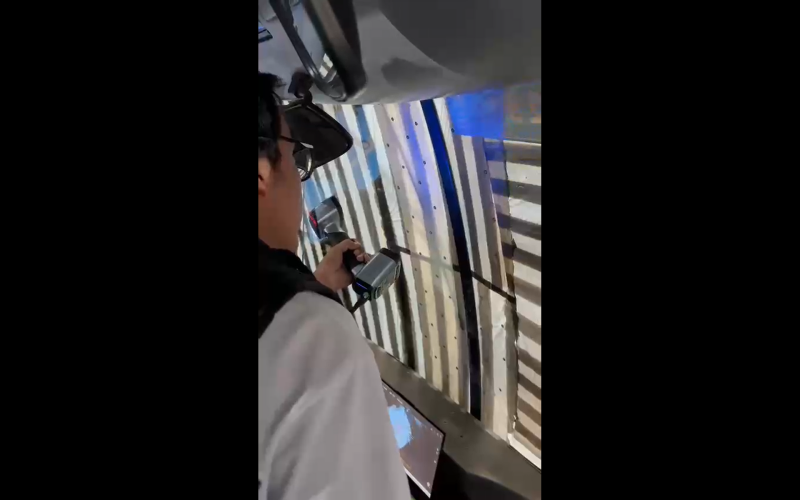
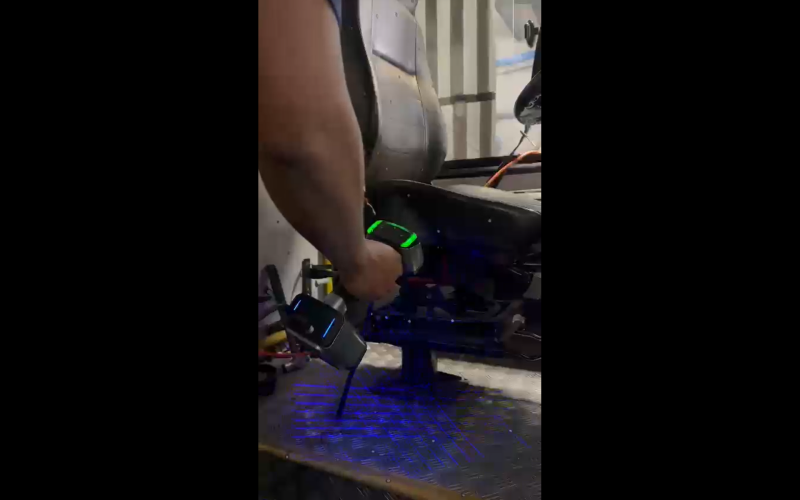
Un technicien en train de numériser l’habitacle d’un des bus.
Le EinScan HX a également permis à l’équipe d’obtenir des mesures avec une précision de 0,04 mm. Grâce à ces mesures précises, l’équipe BSTAR a pu concevoir une cloison qui s’ajuste parfaitement à la forme du bus.
La numérisation 3D pour la réfection de cloisons de bus était sans aucun doute une option plus efficace que la mesure manuelle de la zone. De plus, les mesures manuelles laissent place à l’erreur, comme peuvent en témoigner les chauffeurs de bus.
Après une session d’environ 3 heures (comprenant le retrait des pièces inutiles, le collage des marqueurs et la numérisation 3D), le technicien de BSTAR a obtenu un nuage de points 3D propre et précis de la cabine de pilotage :
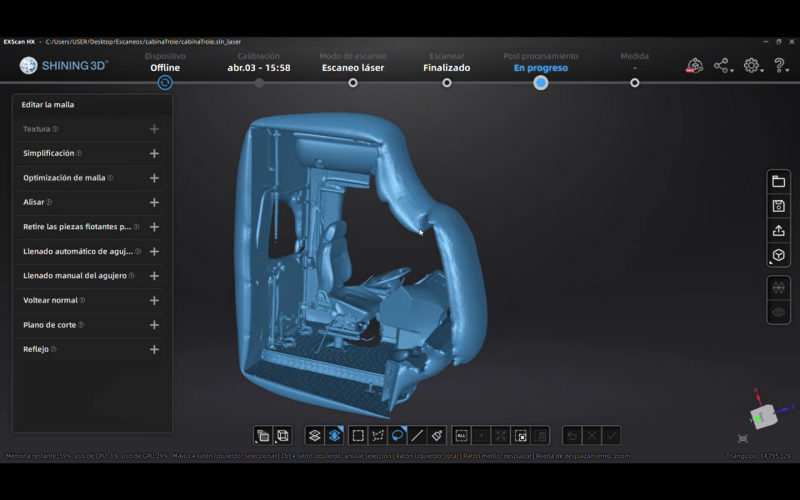
L’équipe a ensuite exporté les données vers Solid Edge, un puissant logiciel de conception 3D. Grâce à ces données, ils ont pu redessiner la cloison du bus. Ils ont veillé à ce que la taille de la partition soit correcte et qu’elle n’occasionne pas de nuisances sonores pour les conducteurs.
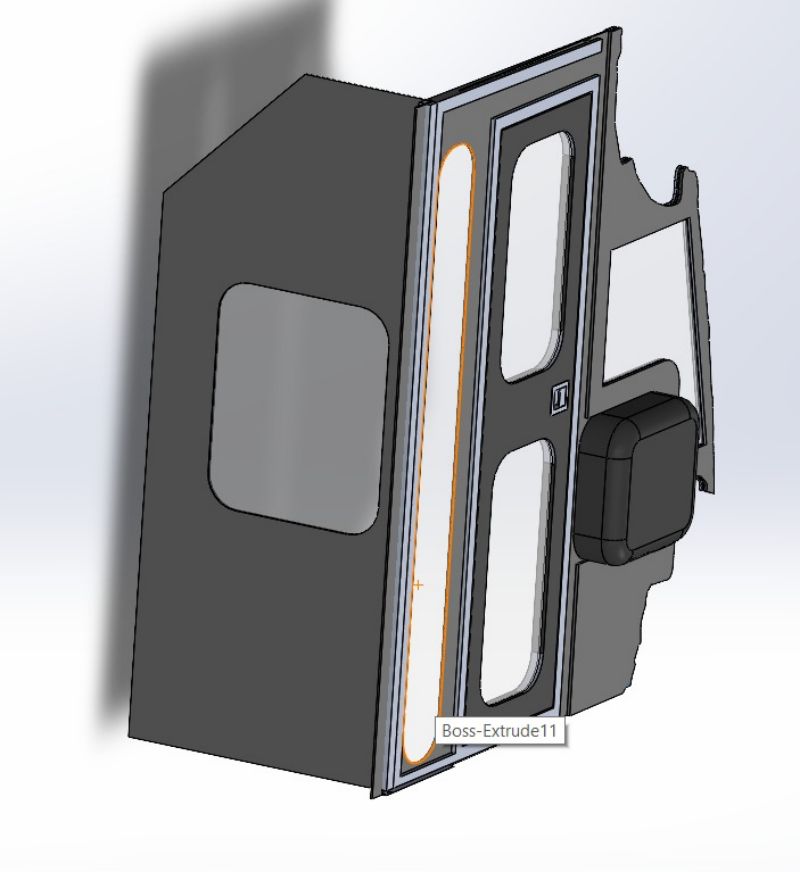
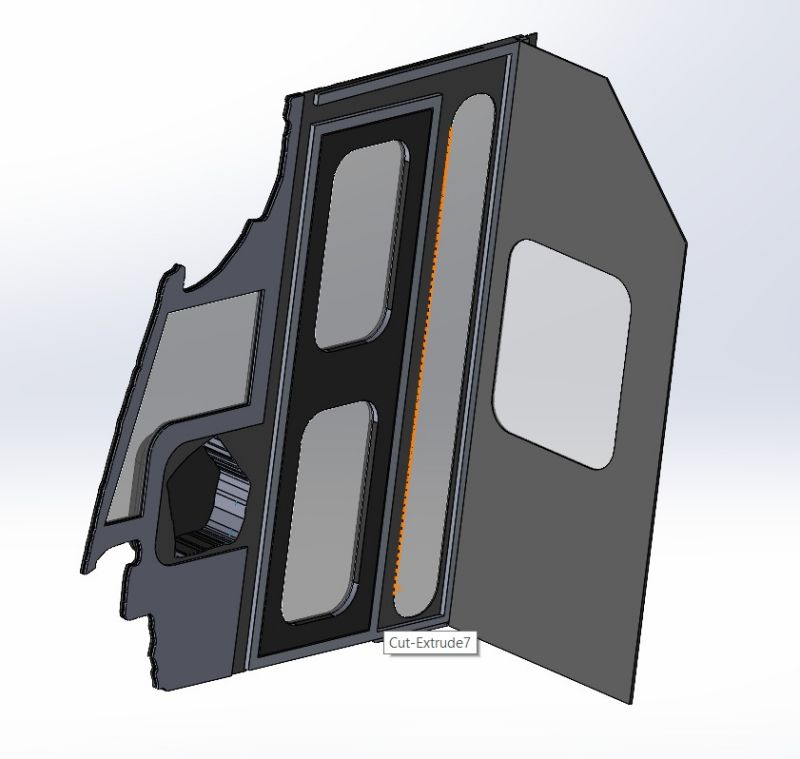
Le modèle 3D des nouvelles cloisons.
La nouvelle cloison sur mesure doit être produite en série et installée sur les 800 autobus.
Conclusion
Les chauffeurs de bus de Quito ne supportaient plus le bruit incessant provenant des cloisons mal conçues. Ce bruit affectait véritablement leur audition et leur bien-être au travail, et cette nuisance était présente dans des centaines de bus.
Grâce à la numérisation 3D et aux logiciels de CAO, l’équipe de BSTAR a pu remodeler les cloisons et assurer un environnement de travail plus confortable pour les chauffeurs. La portabilité et la précision du scanner EinScan HX, ainsi que les puissants outils de conception de Solid Edge, ont été des alliés essentiels dans cette tâche.
Vous avez besoin d’optimiser des pièces critiques dans votre domaine d’activité ? Contactez nos spécialistes pour un entretien gratuit et découvrez comment nos scanners 3D précis et efficaces peuvent vous aider.